
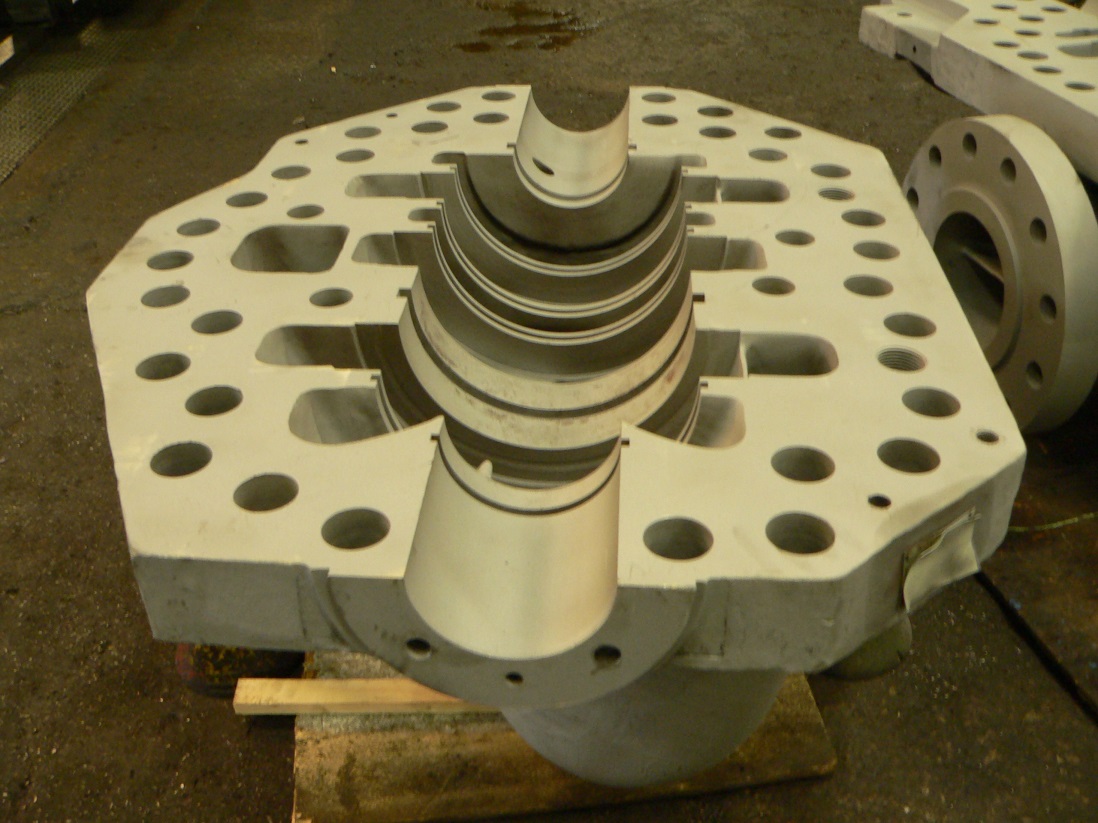
Image: 4074658 © Robyn Mackenzie / ĭana Trousil is a StarFish Medical Manufacturing Engineer. In the drive to production, it’s important to understand the volumes involved, and align expectations of what your chosen production process can achieve.
#Production tool full
A good paint shop can do fantastic finishes with only low volume, but it’s not the same as a full production line where the processes are fully controlled. Note that these processes require painting, which has its own low-volume production issues. If your volumes aren’t high enough, consider using other processes like Reaction Injection Molding (RIM), cast urethane (silicone rubber moulding – SRM), or even machining. Injection moulding, even prototype tooling, can still be expensive. Not controlling the heat of the plastic can result in part defects like gloss, weld lines, warping, or even mechanical properties. Why are cooling lines important? They affect the heat of the tool, and therefore the heat of the plastic. Designers may have to take on more of the design of the tool, reviewing or performing mould flow analysis, or even reviewing cooling lines, the latter is often much poorer in prototype tools than in a full production tool. There are numerous prototype tooling injection moulders out there, but it’s important to recognize that their expertise may not match the expertise that a full production shop has. Glass-fill materials also cause more wear and maintenance. P20 requires a bit more care in maintenance to ensure the tool doesn’t rust in the meantime. While costs are minimal over large runs, the smaller runs of typical production start-ups may mean that a tool is run once, then shelved for six months. Injection moulding parts are cost effective, but there is a significant set-up that’s usually rolled into the cost of the parts. Factory machine operator Machinist Tool and die maker Production operative. Telephone: (800) 236-6020 Fax: (586) 755-6633 Website: Website. There are several names for the modern manufacturing tool maker but they. P20 is often used as a cost-effective tool, but the steel may see more wear over time. Street: 8655 Eight Mile Road City: Warren State: MI Zipcode: 48089. A lot of injection moulders simply choose not to work with aluminium because the cost savings compared to P20 steel tools aren’t that great with off-shore tooling, and there are significant compromises with aluminium tools.

Aluminium tools have the advantage that machining is easier, but it comes at the cost of not having the same thermal mass and cooling as a standard steel tool. Prototype injection moulding comes in a couple of forms, namely aluminium or steel tools, like P20. In this blog I’ll concentrate on injection moulding, but there are analogs for other processes.
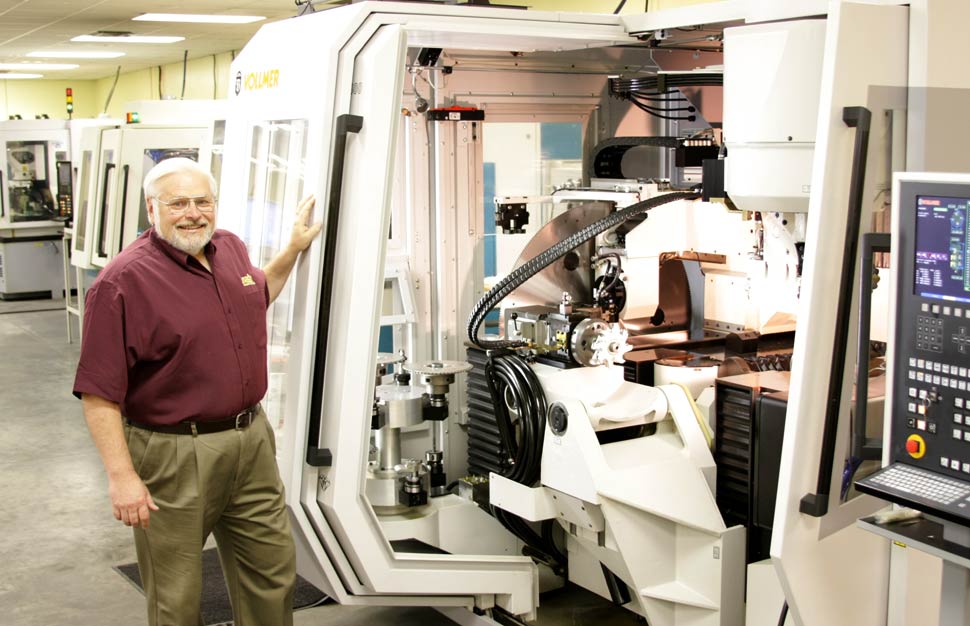
So what does one get with “prototype” tooling? The answer can be “a lot”. Tooling for any product can be very expensive, and without knowing how many will be sold, the return on investment (ROI) for the capital expense of tooling may fall into a grey area – maybe the ROI will be acceptable if volumes are high, but maybe not if we don’t hit the sales we think we could.įull production tooling is expensive and a lot of the time can’t be justified. The best answer begins with other questions: “What quality do you really need?”, and “How many are you making?”Īll products have a life cycle, and graphs like these can be seen in various forms:įor start-ups of unique medical devices, there often isn’t even a similar product in the portfolio that the the initial slope can be estimated, and so we’re left with a best guess. 943-971.Dana Trousil in Manufacturing | No comments Prototype vs Production tooling “What’s the difference between production tooling vs prototype?” and “What quality can I expect?” are often questions that I get asked from development or clients. and Sriyanto (2020), "Manufacturing sustainability assessment using a lean manufacturing tool: A case study in the Indonesian wooden furniture industry", International Journal of Lean Six Sigma, Vol. Hartini, S., Ciptomulyono, U., Anityasari, M. They also acknowledge the efforts of the reviewers. The authors are grateful for the financial support from Diponegoro University. Manufacturing sustainability assessment.The visualization of indicators through sustainable-value stream mapping is proven to be more practical and helpful for industrialists. The selection of the indicators has involved practitioners in the furniture industry and encompassed economic, environmental and social dimensions. The value of this research lies in the novelty of the single index in measuring manufacturing sustainability and the relevant indicators for the furniture industry in Indonesia.
